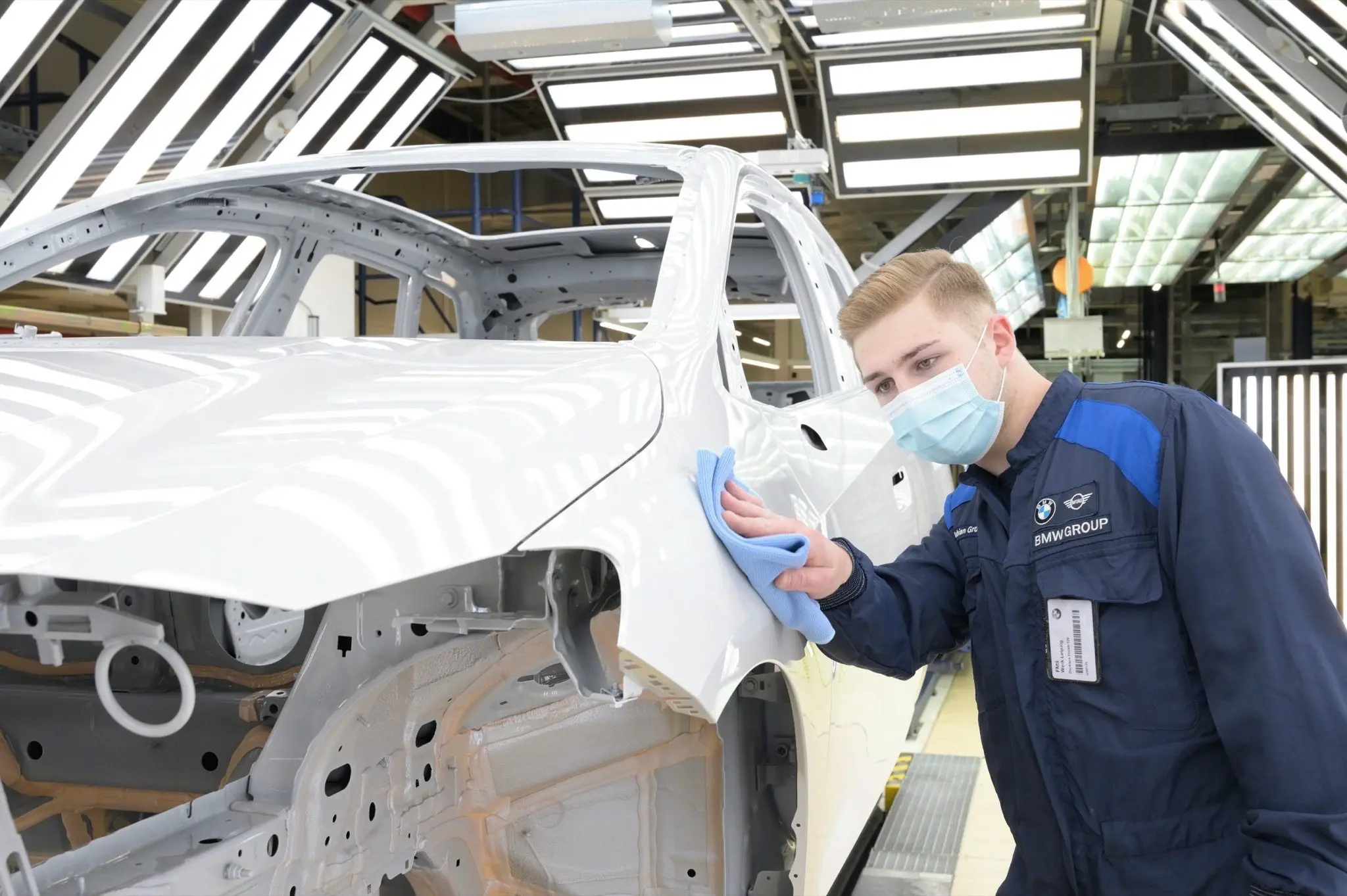
BMW Group continuă să reducă emisiile de CO2 în reţeaua sa de furnizori, ca parte a activităţilor sale ambiţioase de dezvoltare durabilă. Oţelul produs folosind gaze naturale sau hidrogen şi energie verde, în loc de resurse fosile precum cărbunele, are o contribuţie vitală la acest lucru. Acum, BMW Group a semnat un acord cu Salzgitter AG pentru livrarea de oţel produs cu emisii scăzute de carbon. Oţelul va fi utilizat în producţia standard de automobile la uzinele europene ale BMW Group începând cu 2026. Prin această colaborare, BMW Group îşi extinde aprovizionarea cu oţel produs cu emisii scăzute de carbon la doi furnizori. Obiectivul este de a folosi oţel produs cu emisii scăzute de carbon pentru a acoperi peste 40% din cererea uzinelor sale europene până în 2030, reducând astfel emisiile de CO2 cu până la 400.000 de tone pe an.
„Acesta este un pas important în reducerea substanţială a emisiilor de CO2 la sursă în reţeaua de furnizori”, a declarat Joachim Post, membru al Consiliului de Administraţie al BMW AG, responsabil pentru achiziţii şi reţeaua de furnizori. „Obiectivul nostru este de a reduce amprenta de carbon pe durata de viaţă a automobilelor printr-o abordare completă. Cu oţelul, în special, suntem lideri în ceea ce priveşte aprovizionarea cu emisii scăzute de carbon pentru uzinele noastre din Europa în viitor”.
De asemenea, BMW Group se va aproviziona cu oţel produs folosind hidrogen şi energie verde din nordul Suediei pentru uzinele sale europene începând cu 2025, reducând emisiile de CO2 cu până la 95%. Uzinele de presă ale BMW Group din Europa procesează peste jumătate de milion de tone de oţel pe an.
Datorită procesului său de producţie care este mare consumator de energie, producţia de oţel generează emisii mari de CO2. Cu toate acestea, datorită versatilităţii sale, oţelul este unul dintre cele mai importante materiale pentru producţia de automobile şi va continua să reprezinte o mare parte din caroserie şi multe componente.
Pentru a reduce cu un nivel important emisiile de CO2 din producţia de oţel, Salzgitter AG trece treptat la producţia aproape fără nici o emisie de carbon. Electricitatea din surse regenerabile şi utilizarea acesteia în producerea hidrogenului din electroliză sunt elemente-cheie ale transformării. Hidrogenul verde va înlocui cărbunele utilizat în prezent în procesul convenţional de furnal. Acest lucru este posibil prin aşa-numitele instalaţii de reducere directă, care utilizează hidrogen pentru a reduce direct minereul de fier în fier în stare solidă. Fierul solid produs în acest fel este topit apoi cu resturi de oţel într-un cuptor cu arc electric alimentat cu energie electrică regenerabilă.
Salzgitter AG intenţionează să folosească această metodă pentru a reduce treptat emisiile de CO2 din producţia de oţel la doar 5% din nivelul iniţial.
În urmă cu mai bine de cinci ani, împreună cu Salzgitter AG, BMW Group a stabilit deja un ciclu de materiale cu circuit închis pentru deşeurile de tablă de oţel de la uzina BMW Group din Leipzig. După livrarea bobinelor de oţel către fabrică, Salzgitter AG preia resturile de oţel de tipul celor produse la fabricile de presă – de exemplu, atunci când uşile sunt perforate – şi foloseşte acest material pentru a produce oţel nou. Apoi, acest oţel este furnizat uzinelor BMW Group. În acest fel, materiile prime pot fi folosite de mai multe ori într-o economie circulară, conservând astfel resursele naturale.
Deşeurile de tablă de oţel de la celelalte uzine europene ale BMW Group sunt, de asemenea, fie reutilizate printr-un ciclu direct al materialelor, fie trimise înapoi producătorului de oţel prin comercianţii de oţel şi procesate în oţel nou.
Până la un sfert din oţelul din automobilele BMW Group provine deja din circuitele de reciclare. BMW Group intenţionează să-şi crească procentul de oţel secundar în etape, ajungând până la 50% până în 2030.
Deoarece aceasta necesită mult mai puţină energie, emisiile de CO2 din producţia de oţel secundar sunt în medie cu 50-80% mai mici decât cele de la oţelul primar.
Investiţiile în companii start-up accelerează dezvoltarea de noi tehnologii
Pe lângă aprovizionarea cu oţel cu emisii scăzute de carbon, BMW Group a investit şi într-o metodă inovatoare de producţie de oţel fără carbon dezvoltată de compania start-up americană Boston Metal, prin fondul său de investiţii BMW i Ventures. Boston Metal foloseşte electricitate pentru noua sa tehnologie, care, prin intermediul unei celule de electroliză, produce fier topit care ulterior este transformat în oţel. Dacă pentru acest proces se foloseşte electricitate din energii regenerabile, atunci producţia de oţel este fără carbon. În următorii ani, Boston Metal plănuieşte să extindă noua metodă de producţie a oţelului la scară industrială.
Prin investiţia sa în companii start-up, BMW Group îşi propune să accelereze dezvoltarea noilor tehnologii, să promoveze concurenţa şi să ofere un impuls care va facilita intrarea pe piaţă a companiilor tinere. Tehnologiile inovatoare oferă un acces mai bun, mai durabil şi mai eficient la materii prime.
Investiţia în noi tehnologii este unul dintre mulţi paşi pe care BMW Group îi face pentru a-şi îndeplini obiectivele ambiţioase pentru lanţul de aprovizionare cu oţel – de exemplu, făcând producţia cu emisii scăzute de carbon un criteriu important de atribuire pentru fiecare contract